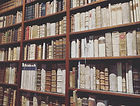
BINDING
THE START
When books were only wax tablets held together on rings, it functioned more in the way of utility, but as the development of paper and ink became widely used, and the easily destroyed paper needed protection, binding as we know it today (cover, end-sheets, textblock, etc) became an art that used the specialized skills of different craftsmen to create it. Skills with certain materials developed in different areas of the world, from China to England, and the availability of those materials depended on that region. Coverings were often made from leather, dependent on the
animal available, and the sewing techniques can be identified down to the person, place, or time period.
There are many different ways to bind a book, reliant on size, paper, region, and often (almost always) the binder. Basically every binder has a different way to produce the same result, though there are always ways of finding out what it is that was done, especially if you come across a broken book. The following bindings are the most common and most well known, and often the cover addition is the same, especially for the more popularly used techniques now.
COPTIC BINDING

Coptic binding is one of the oldest binding techniques, done first by early Christians in Egypt from the 2nd to the the 11th centuries, creating the first true codicies, or what we think of as books now (textblock and cover together as one piece). It is one of the simplest and prettiest of bindings, since you can see the sewing done on the spine of the book. There is no typical spine as we think of it on a coptic sewn book (i.e. no spine covering) and so the technique of the sewing is visible and easy to recognize.
To make a coptic binding, you will need the
number of signatures (folded pages) you want, the back and front cover, a needle, and thread. You will need to punch holes, usually with an awl or other sharp implement, an equal distance apart on your signatures and cover boards, most requiring five though it can be done with fewer. Stack the covers and signatures how you want them to be when finished, basically forming the book before sewing (back cover, signatures, front cover) and thread the needle without tying off. You want to have the thread about three inches through the eye of the needle to make sure it’s secure every time you pass it through the book. Then you will thread the needle through the back cover bottom hole, pulling
through until you have about a handful length of thread left on the entrance side. Tying a knot here will help make sure that you don’t pull too much through and make a secure foundation for the rest of your book.
Once the knot is tied, thread the needle once more through the same hole to have two pieces of the thread visible on the cover’s spine side. Then poke the needle through the first signature’s hole above the board’s hole you just went through, and then moving to the next hole in the signature to then go back through the board and the hole corresponding. You only want to be sewing on one signature at a time. Repeat through the five holes and when you have reached the end, thread the needle through the cover twice to match the others (you will always be wrapping around the cover twice), making sure to keep it tight, and add the next signature on top. Pass the needle through the next signature as you did with the first and when the needle comes out towards the spine, thread the needle around the stitch right below the one you are making (not into the signature or board, but just around the thread of the stitch directly below), to secure it and then go back into the hole you
came out of, repeating down until the end of that signature. Repeat the process until all of your signatures are sewn, and then attach the front cover by passing the needle and thread through the top of the closest hole at the bottom of the cover and passing it through twice, and go back into the signature through the hole you came through and do the same through the whole cover. Once you reach the end, pull the needle back through to the inside of the cover and pass it through itself once or twice and then tie it off to make everything secure and tight.
To see this process done by Jim Escalante, click on the video to the right.
TAPE SEWN BINDING
This process is one of the most common, especially during the 18th-20th centuries as book production became more widespread. There was also a process during these periods called “laying-on” which functioned from the same principle as tape sewing but used cords instead of “tapes” to sew the pages to, making the raised bands on the spine that we see on many books of these periods. The tapes are made from closely woven strips of cotton, usually 1/2 inch to 1 inch across, and suspended from the sewing press. In most cases, there are only two to four tapes used, but for larger books that need more support a larger number will be used.
Holes will be made in the signatures that basically outline the tapes so that the thread can be pulled through one hole, across the tape, and through the other hole on the other side, and most of the process that was used in the coptic binding is applied here, though in variations in certain areas of the world (mostly Europe), though the tying off and securing is different. The way these holes are made can be done by sawing into the spine side of the whole text block, or poking holes individually. There will also be holes made for the catch-stitch that enables the binder’s needle to “turn around” and go back through the book.
To see this process done in full by Bookbinder’s Chronicle, click on the video below. I suggest watching it at 1.5x or 2x speed.
OVERHAND SEWING
This is the process used by most binders and bookmakers today, as it is the simplest way to secure a book. It requires a glued text block, so one where the signatures have been perfectly aligned and then glued along the spine. Then, either using a binding drill or a hand drill, holes (usually 4-6) are created equally apart right next to the edge of the spine on the text block, though not so close as to be on the spine and no so far as to make it impossible to open the book when finished. Then a needle and waxed thread is taken through one of the middle holes from the bottom, threaded through the top and to the next hole on
the top, and the process repeats until you get to the end of the entire text block, shown through the illustration below. The thread finishes at the hole directly next to the hole you started with so that the thread can be pulled tight and then tied off. From there you can then give the text block any spine support or super that it needs and case it. This is the process that I use in both my conservation (if needed) and the creation of new books at the bindery.
7th 6th 2nd 3rd
8th 9th 1st 4th
&5th
COVERS & CASING
Making covers has pretty much been the same process since the end of the 19th century as it is today, though materials have obviously changed. Because none of the books on this site were made through any medieval processes (i.e. old leather processes and certain types of decoration), I will forego explaining them, but they can be found here.
First the text block has to be prepared to be covered once it is sewn. This includes adding endpapers, which is a simple process but if the text block is not being cut again, which often is not done during conservations, the endpages must be folded and then cut to match the size of the text block carefully. These are then pasted to the textblock along the gutter edge of the first page and labeled with either an f or a b, in the correct position, to show which side is the front and which is the back. Headbands can also be added at this stage, which are simply pasted on the head and tail of the textblock. The spine is given a paper support, glued directly onto it, with super, or thin cotton mesh, applied to it and pasted down to the endpapers. This secures the endpages to the text block, and the labeled endpage will then be the piece that secures the textblock to the cover.

The basic way to make a cover requires boards that match the text block and leave a lip on each side except the one closest to the spine, a material to cover the boards in, a spine support the same size as the textblock spine made either of paper or board, and glue, often white glue (think Elmer’s but stronger). The spaces that are needed between the boards and the spine support are measured to match how it should rest on the book, and the material is cut to size, ensuring about an inch all around the boards so that the material can be pasted to the inside of the board. Once all the correct alignments are marked for the boards and spine support, the material is spread with glue on the back side and the boards and spine support are placed back into their positions. The corners are snipped at a slight angle so
that when they are folded they lie flat against the inside of the book. A bone folder is used to press the boards and support down carefully and also applied to pull the material over the edges of the boards and pressed to adhere. This is usually done by pulling the top and bottom first and then the sides, pressing especially a the corners. Then the cover is turned over and given a few good swipes with the bone folder to make sure there are no bubbles or problem spots. It is left to dry until you are ready to case the book (put the cover on the text block).
The casing of the book is relatively simple but requires the most precision and patience. The text block is placed in the dry cover to line up where it needs to rest. It is then carefully held there, the text block in the place it needs to be on the back cover with the front cover open, while the top endpage is spread with glue. The front cover is then slowly folded onto the endpage and pressed gently to adhere. The binder then flips the book over so that the majority of the text block is now on top and opens to the endpage that they have just pasted down to check the edges are equidistant from the sides of the book and in the correct placement on top and bottom, and then the endpage is softly pressed down with a cloth or bone folder to make sure it adheres in the correct spot. The same process is done on the back and then the book is left in the press until the glue is dry. When it is done, you have a finished book!
EMBOSSING & STAMPING
The stamping process comes well before the embossing one, but the idea is the same: decoration and labeling. Binders would have special tools, rollers with designs on them, special blunted knives, or even actual carved “stamps” to make designs on leather and cloth covers in earlier centuries, often doing the decoration after the book was made. Now the process is highly mechanized and uses mostly heat to make impressions in the cover material, and is almost exclusively done on the cover as a separate piece. Blind embossing, or stamping, simply means that there is not color to the decoration, and is left “blank” to create an impression on the cover. Combination embossing is the most popular one, as it
requires something between the machine or tool and the cover, usually gold or silver leaf. Often the same kind of typeface that is used to print (and so moveable type) is used to put labels and names on books today. The machine now is one that requires the type or die cut (a design or stamp made as one piece of moveable type) to be placed into a composition stick, or slug, and then onto the machine that is heating the metal type up to a high temperature to make the gold or silver leaf stick to the cover correctly. The type is centered and the cover is aligned on the machine and the lever is pulled to bring the type down on the cover. This process requires practice to get the best looking label, applying the correct amount of pressure and time to the lever. Once done, the cover can be added to the text block and the book is finished!
To see traditional gold tooling done, without the machine of today, from Kennys Bindery, click on the video above.
To move through the topics, click on any of the buttons below. To go back to the main page, click on the books in the top left corner.
All works used are listed in the bibliography under this topic's title heading.