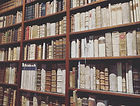
ILLUSTRATION
THE FAB FOUR
Decoration and illustration of books is not a new concept and has always been a large part of learning languages, plots, and often describing what cannot be done any other way. Illuminations in early manuscript culture were a way of mostly decorating the page, making the book more object than text in its beauty. As illustration developed as an art it started to describe the text more often, “illuminating” what the text was trying to say. Early modern books emulate illuminated manuscripts often, as print culture was so new, but with mechanized production of books would of course come mechanized and new ways to print illustrations and illuminations. There are four main ways to produce pictures on paper: relief printing, intaglio, lithography, and stenciling. The last is not often used for books or small productions, and all but the last must have the illustration done backwards on the surface to be printed from, just like typeface, so that it appears correctly on the page. I will be talking about the first three here.
WOODCUTS
Woodcuts, a form of relief printing, were the most common during the early years of printing, as they were easy to make, disposable, and worked with the oily ink that was required for the metal typeface quite well. Woodcuts had been used by the Chinese before anyone else as a way of producing pages of the same characters for their early print culture, but in the Western world woodcuts were often limited to everything that typeface couldn’t do: draw. The process of woodcuts is simple enough to understand; it’s basically in the name! A piece of wood, often one that is leveled flat on one side (and would fit into the coffin of the printing press at the correct height) would be carved on the opposite side in relief, meaning that everything around the illustration, or at least the pieces that were not to be printed, were carved away. Basically, to create a blank space you carved, to create an inked space, you left it and carved around. Ink is then added to the raised illustration, and it is covered with the piece of paper you want to print on, and either pressed under the press or given pressure some other way, sometimes a spoon! The print is successfully transferred to the page this way, and if more than one color is needed on the page specifically from the woodcut, a different woodcut to match was often made and carefully placed so that the ink would go where it should.
Woodcuts are best identified by the bleed they give off on the page, the ink distribution, or the lack of minute detail that most have, simply because using the same woodcut over and over can make it wear over time, with constant pressure and moisture from the ink. MOMA, the Museum of Modern Art in New York City, has created a brilliant game-based exploration of the four different processes of printing. As an interactive piece, it is demonstrably better than simply reading a wall of text, so I suggest you click on the button below to take you to their site. Remove any pop-up blockers you have, otherwise you can’t play the game!
INTAGLIO
As the desire for more detailed printing on a large scale came into play, printers looked for better ways to faithfully render illustrations on the page in many different copies. Intaglio printing, of which etching is an example, was first developed in the 16th century when it was found that acid could be used to create grooves in prepared metal. It’s done by first painting the metal plate to be used with an acid resistant waxy substance referred to as “ground,” and then after it is dry an etching needle is used to draw the image and carve down to reveal the metal beneath the ground. This allows for detail to be etched into the image much more precisely than woodcuts can produce. The artist or engraver must remember that the grooves they are creating will be the part filled with ink, so basically reversing the woodcut mentality and carving for ink, rather than carving away for it. Once the engraver is done drawing the metal plate is put into a bath of acid where the acid will be repelled from the portions with “ground” still on them but will eat away at the etched areas, creating deeper grooves for the illustration. When the grooves are determined deep enough, the metal plate is removed from the acid and the “ground” is wiped away with a solvent that cleans it without hurting the plate. The plate now only bears the composition. The entire plate is inked
and dabbed a little heavier over the engraved spaces to make sure that ink is evenly and well distributed, and then the ink is wiped from the surface carefully so that only the ink in the grooves is left. The plate is then placed face up on an etching press (usually a roller press) with a piece of dampened paper laid on top to be able to attract the ink, and with a piece of padding (felt usually) is rolled under the press to force the ink up onto the paper, and the image is left on the page in reverse. Different colored ink could be pressed carefully in the grooves if needed by ink balls or cloth gatherings, but could also be done with pin holes created before printing to register exactly where the page must go in order to be inked twice. You can often tell that an image was made with the etching or intaglio method by a plate mark appearing on the page, where the edges of the plate have pressed into the page because it requires a significant amount of pressure to get the ink to raise to the page. Click below to play MOMA’s game for this process as well.
LITHOGRAPHY
Lithography, developed during the late 1700s but widely used starting
in the 1860s, was the most direct way of getting an image on the page because the images are rendered much like you would draw with watercolors or crayon, and could be far more artistic and freeing than etching or woodcuts. Drawing directly onto polished limestone with tusche, a specific kind of greasy wax crayon used for this process, the artist creates their image. The stone is then treated with a chemical solution that makes the greasy image attractive to the greasy ink while the blank areas will repel the ink and rather attract water. The image is then “fixed” or securely bonded to the stone using a solvent, sometimes turpentine, that dissolves most of the original drawing but leaves a “ghostly” image on the limestone of the greasy illustration. The stone is made damp with water, which only the blank areas hold onto, and then rolled over with greasy ink, adhering only to the image. The stone is then set onto the lithographic press
with a sheet of damp paper on top of the image and made steady with a piece of board and rolled under the platen, or flat and heavy part of the press and given equal pressure. Separate stones could be used for each color, like with intaglio printing and that is where color printing for this process started, but eventually it developed to a point where, in the 1830s, chromolithography, or color printing, was able to be done simultaneously. This was produced by offset-indirect printing, where the stone is “registered” or given precise measurements within the press and an outline image, rather than the key detailed image, is used to register each run through the press, and therefore print of a different color, was placed correctly every time until the final key image was printed onto it, reversing the order of color printing of the past and making it more precise. This process was developed further later on to produce almost identical renderings of photographs in newspapers and books.
Lithography is often colorful and much more modern looking than either intaglio or a woodcut and the same basic process of offset-indirect
printing is still used today in print culture, though more often on what we see on things like yogurt labels, toothpaste, and other products. To play MOMA’s game with this process, click on the button below.
Now, illustrations in the digital space are created easily through digital printing, which basically draws the image on the page for us, and putting a photograph on a page is so easy in comparison to the time it took not even 50 years ago to do the same. The Folger Shakespeare Library, countless special collections libraries, and many other institutions have holdings of woodcuts, lithographs, and intaglio metal plates that give us great examples of just how much artistry and careful understanding of the process it took to create books of the past.
To see how modern offset-indirect printing is done, click on the video to the left from Express Cards, an Australian printing company.
All works used are listed in the bibliography under this topic's title heading.
To move through the topics, click on any of the buttons below. To go back to the main page, click on the books in the top left corner.