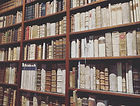
PAPER
HISTORY LESSON
Essentially, paper is a smooth, flat substance generally made from cellulose fibers closely woven together from a fibrous material. The fibrous material the Chinese used when they began making paper about 104 A.D. was probably a mixture of bamboo bark, mulberry, and other vegetable fibers. It is assumed that it was first made by spreading the wet pulp mixture of these onto a woven cloth to dry and then was lifted and used. Two centuries later they shifted to using thinly cut, closely laid bamboo lined trays dipped into a vat of the same kind of wet pulp mixture. The water ran off when lifted but the pulp stayed and was laid out to dry.
Eventually paper making spread to Europe in the 11th century, where they used mostly parchment (also called vellum) made from animal skin that was stretched and scraped. The process of making paper in Europe was basically the same as in China, except that it was made almost exclusively from linen rags washed and mashed into a fibrous pulp, often called stuff. This was then transferred into a vat filled with water and passed through straining trays lined with flat iron wires. Passed through a few times and shaken, allowing the water to run off the newly created sheet of rag paper, the sheet was then left to dry.
Italy took to paper making in an innovative way and formed new ways of making paper toward the end of the 13th century. A stamping machine run by a water wheel replaced the mortar usually used to mash the pulp, and the bottom of the moulding trays were made of round rather than flat wires as before, making the paper much more thin and flexible, where they had once been rough and long-fibered.
The paper sheet made in this tray was then couched against a piece of woolen felt, firmly pressed onto it so that the sheet lifted from the bottom of the tray, so that the tray could be used again. Another piece of woolen felt was placed on top of the couched sheet of paper so that the process could be done again and piles were made in this way. Once the pile was large enough it was put into a screw press and squeezed to remove excess water. The same process was done again using new wool and then the paper sheets were hung up to dry. Dried sheets were then dipped into a solution of starch to make them non-porous to ink, so that the ink would stay on the page where it was put, and then glazed after further drying.
The video above shows the usual process for rag paper production, done by the University of Iowa's Center for the Book, a little more modern but still mostly similar to how it would have been done, including the dying and sizing process, trying best to emulate paper made during the early periods of paper making in Europe.
Nowadays, paper is made almost exclusively by machines, and almost always out of wood-pulp using the same kind of method but much more mechanized, as it is the cheapest and easiest to produce, though it creates a very brittle and easily oxidized paper because of the highly acidic resin that the wood contains. To see how most modern paper is made, watch the video below from PaperOne.
The wood is stripped of its bark and chipped, and from there chemically fermented or pulped to get it down to the consistency that will work for the machines to spray it and slosh it across large frames. Without the finishing process comes the paper we know from newspaper, but to be made into more useful paper, like what we print from, it has to be finished. This involves a larger process, though a similar one, of the pulp being sprayed and sloshed through large (enormous) frames and then alternately dried and squeezed to remove water. It is then rolled into massive rolls and cut into smaller and smaller pieces to produce the stacks we're used to. Glossy, thick, thin, and
other types of paper have slightly different processes and finishings, but all begin the same.
SPECIAL PAPER
Text pages are not the only pieces of paper that compose a book. Endpapers are just as important for the stability of the book and have routinely been used as decorative pieces of the text. Books like Baedeker's Handbook to London include endpapers that have been printed on, while other books have illustrated end-pages or ones that are decorative in some way. Marbled paper is one of the more popular designs for both the inside and outside of covers. Powdered alum, aluminum sulfate, is dissolved in water and then painted over the paper that is going to be marbled. Carrageenan, a gelatin powder made from seaweed, is then blended with water to make size, which is thicker and can hold the paint on top of it without letting it spread too far. This mixture is poured into a tray or frame larger than the paper that's going to be marbled. Paint is then thinned with water and sprayed dropped into the filled tray. You're able to create patterns with rakes or brushes and then place the paper lightly on the side that was covered with alum onto the paint, lift it gently, and let it dry. The video below shows this process as it is done by hand by artist Rene Eisenbart.
CONSERVATION
Most paper conservation techniques that libraries and museums use requires a lot of knowledge about the chemical composition of the paper you're working with and just how much you are able to manipulate it. In the personal world of conservation however, there are simple techniques that mimic those of the scholar world that do not either ruin the paper or put it in jeopardy for the future. Though asking a bookbinder or conservationist before doing it to any book you own would be better than reaching for the scotch tape you think should work (IT WON'T! DON'T DO IT I'M WARNING YOU). Scotch
tape actually ruins and stains the paper it's on over time, no matter what type of paper it is, and will pull up ink if you try to remove it.
The kind of tape that is used in my bindery is more like a huge roll of heat-set tissue paper. It also comes in a scotch-tape sized roll, for smaller tears, but when you need to cover a page in it to keep the page intact it's nice to have a large roll. It is usually made from mulberry fibers, like the Chinese initially used for paper, because it can be made thin and flexible, with one side a sort of adhesive that is meant to stick to the page when heat is applied.
Of course there are other conservation techniques, including gum-paste or wheat-paste adhesive, mending tissue also made out of mulberry but adhered with water, and methyl cellulose, which is acid free and easy to use for small tears. There are whole schools devoted to the art of conservation and classes in art departments that focus on paper as a concentration. Conservation is obviously important in libraries and museums, but it is also important for families holding on to history and to personal artifacts staying whole on shelves.
To move through the topics, click on any of the buttons below. To go back to the main page, click on the books in the top left corner.
All works used are listed in the bibliography under this topic's title heading.