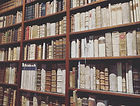
TYPEFACE & PRINTING
YE OLDE PRINT SHOPPE
We have a million typefaces to choose from today, but when printing first was invented, with moveable type, each piece of type had to be made from a punch, a prototype piece of type, backwards and in relief, carved out of metal, and then stamped into softer metal, usually copper, to create a mold, and then that mold is placed on the bottom of a type-case. A mixture of lead and antimony is poured into it to create a piece of type that looks like the punch and will fit the typeface frame. Click on the video below from Zac Richins to learn more about how Gutenberg, the known father of the modern printing world, made his type.
As typeface and printing developed, so did fonts, sizes, and desires for how the words should look on the page. Larger letters were kept above the smaller letters of the same font at the printer's, becoming known as upper and lower case letters, literally named for their position in the case. When type was first developing and replacing early manuscript culture, the typeface emulated handwriting, evolving naturally from it, so certain letter forms and abbreviations continued to be used within typeface and published works as long as they were in manuscript culture.
When a book was to be printed, in the process that only marginally changed between 1450 and the late 1800s,
a manuscript would be bought by the publisher or printer (who were not always one and the same) off of the author and then a scribe would transcribe the manuscript to readable text for the compositor or compiler. The compositor would then set moveable type, which was always backwards in order to be printed forwards, according to the copied manuscript, into a form or frame that was the correct dimensions for the page to be created. The paper was always a large sheet that would
then, after printing, be folded according to the book's calculated dimensions. Because it would be folded, the compiler was not always setting type for consecutive pages. Instead, type was set according to the pages that would be on that side of the paper, as follows to the right for the most popular foldings (same page, flipped from the right side over):
The type would be set according to what side was being printed on. To keep things in order, before pagination became widely used, folios, or folded sheets, were sometimes numbered, or foliated, at the top of the page. There were also catchwords set a the bottom of the page to correspond with the first word of the consecutive page to make sure that the printer knew what page was supposed to sit where. Most books of the early period were also printed with signature marks, which started with A usually and
Folio (fo):
4 1
2 3
Quarto (4to):
1 4
8 5
3 2
6 7
Octavo (8vo):
13 4 1 16
12 5 8 9
15 2 3 14
10 7 6 11
worked through the alphabet (minus I and U, which were often interchangeable with J and V) and continuing throughout the book to mark the leaves (essentially what we think of as a two-sided page) as belonging to a certain gathering, or folded sheet, as follows:
1 4
8 5
A
A3
3 2
6 7
A2
Not always were the signatures given a mark, but usually the first and the last will be, so that you can infer what the others are. The last in the quarto is not often marked, purely because you would recognize that it was both not a part of the one ahead of it, and it was connected to the one previous. When discussing and studying early books that have these marks, these pages are referred to as A recto, A verso, A2
recto, A2 verso, etc. Recto means the front of the leaf, in English books being the one secured into the book on the left side and turned by the right side to the verso, which is the back of the leaf.
On the common press, or screw press (and based from wine presses!), which was widely used until the early-1800s, the type was placed into the bottom, referred to as the coffin, and then the paper put onto the flat plank and secured to it, called the tympan, and a frame folded over it that separated the pages in the correct dimensions for the book to be printed, called a frisket. From there the type was inked using ink balls and the tympan and frisket folded over onto the inked type. The bed of the press was then pushed under the main portion, or the platen and the journeyman, or printer, would pull at the crank hard, forcing the platen down onto the tympan and therefore onto the inked type. It was then pulled out and placed aside to continue using the same type for multiple copies of the book util the next side was to be printed and the process started again. To see this entire process done, watch the video to the right, again by Zac Richens:
TYPES OF TYPE
As printing became more widespread, the creation of new types of fonts, or styles of typeface, both for different languages and for different looks, emerged. The development of Roman typeface, which is the most similar to what we're used to today (think Times New Roman), came about in 1470 when Nicolas Jenson began printing in Venice. Garamond, created for the French language by the French king's printer in 1541, is still a recognizable font today and one which has been developed as a readable digital type, like Baskerville, or have been made specifically for the screen,
like Veranda.
Most fonts are described as either serif or sans serif, which simply refers to the way the lines of the letters end; either they end with a slight dashed projection like this font, Playfair Display, or they don't like this font, Helvetica. Serif, a word coming from the Dutch shreef meaning dash or line, most closely resembles handwriting of the early period of printing, while sans serif, or without serif, resembles what we now think of as, ironically, print handwriting.
Fonts were often advertised during the periods when customers, publishers, authors or the public, were able to decide what they wanted their book to look like. They would print sheets like the one below to advertise them, called a specimen sheet:
This specimen sheet, from 1565, is held at the Folger Shakespeare Library in Washington, D.C. To look at it more closely and learn more about the piece, click on it to read a blog post done by a Folger librarian. This particular sheet was probably used to advertise the typeface for London printers to buy and then use for their customers, rather than an advert for customers themselves, which seems to have become popular as the facets of the book creation world started to fracture off into areas of expertise.
INKING IT
Ink in the early period of manuscript culture was made from organic materials, like plant roots, oak galls (basically empty wasp nests) and ash, as well as powdered gem stones and gold. Often it was a laborious process that required time and a knowledge of the proper ratios of water, substance, and often required heat to render the ink usable and not too thin.
Once the printing press came into play, Gutenberg realized, as the Chinese had, that with movable type you needed ink that would stick to the metal or wood, rather than be soaked up or run off as water-based ink would do. It was good to use on sized (starched) paper because it
was able to hold on to the fibers of the rag paper, but the metal type needed to hold onto the ink before it was transferred to the page, and so Gutenberg developed an vegetable-oil based ink that was more like varnish, made from most likely lamp black (black pigment made from soot) and linseed oil so that the ink was viscous but clung to the typeface and transferred (and dried) easily.
Now, ink is made to dry quickly from digital printers, so the ink cartridges that we're used to are made from either petroleum or are soy based, pigmented with both natural and chemically developed color.
PRINTING MOVES ON
Printing has developed to a point where we are able to print from our own homes, but as recently as the 1980s, newspapers and books and most other print materials were being made with mechanized versions of the original printing press, down to the job of compiler still being a trade job. The Industrial Revolution in England and most of Europe prompted faster printing with steam powered rolling presses and rotary presses that could churn out a million copies of the same page per day (ideal for a world becoming larger and larger by the shipload). Now we are able to have digital printers that take the image from the computer screen fed to them and render it identically through electricity and what is basically drawing on the page to print as many copies of the pages that you could ever want, whenever you want them. We no longer need to fold reams of paper in certain ways, we don't have to use the same typeface over and over if we don't want to, and we can certainly print as large or as small as we want. Most magazines, books, and newspapers use offset lithographic printing, which is more thoroughly described in Illustration, but below you can see how newspapers are made today with this process from Express Cards, an Australian printing company:
To move through the topics, click on any of the buttons below. To go back to the main page, click on the books in the top left corner.
All works used are listed in the bibliography under this topic's title heading.